Quality Driven Production
News
Saki Corporation celebrated
its 30th anniversary on April 8, 2024
>View more
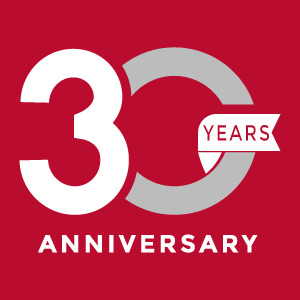
New Award
Saki Presented with Global Technology Award 2023 for X-Ray Systems
>View more
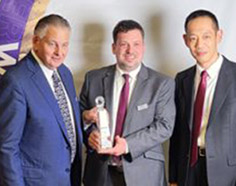
Engineer’s Interview
We interviewed our developers to find out more details about New 3D-AOI
>View more
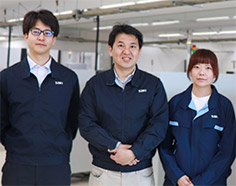

Superior Product Quality
High-accuracy, high-speed and easy to use Saki provides complete inspection solution for any application.
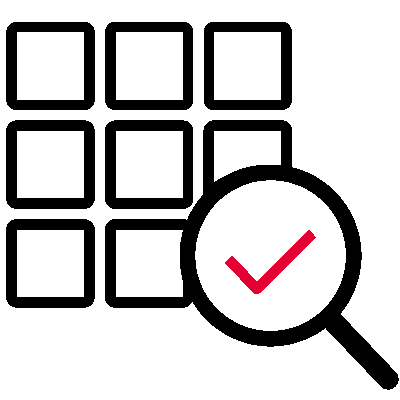
Total Inspection Line Solution
A wide variety of inspections are possible through the development of SPI, AOI, and AXI.
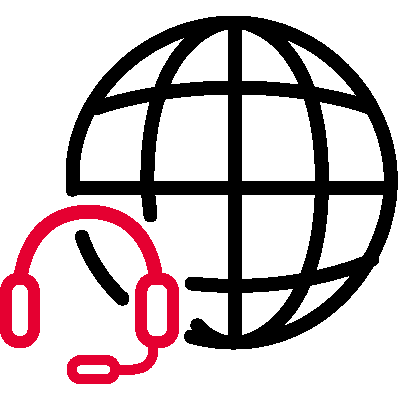
Technical Support Satisfaction Guarantee
Global Customer Support Services network guarantees prompt and efficient response in every time-zone.
Technology
High-speed inspection technology
Saki has attained significant improvements in speed while maintaining inspection accuracy by developing all key technologies of products in house.
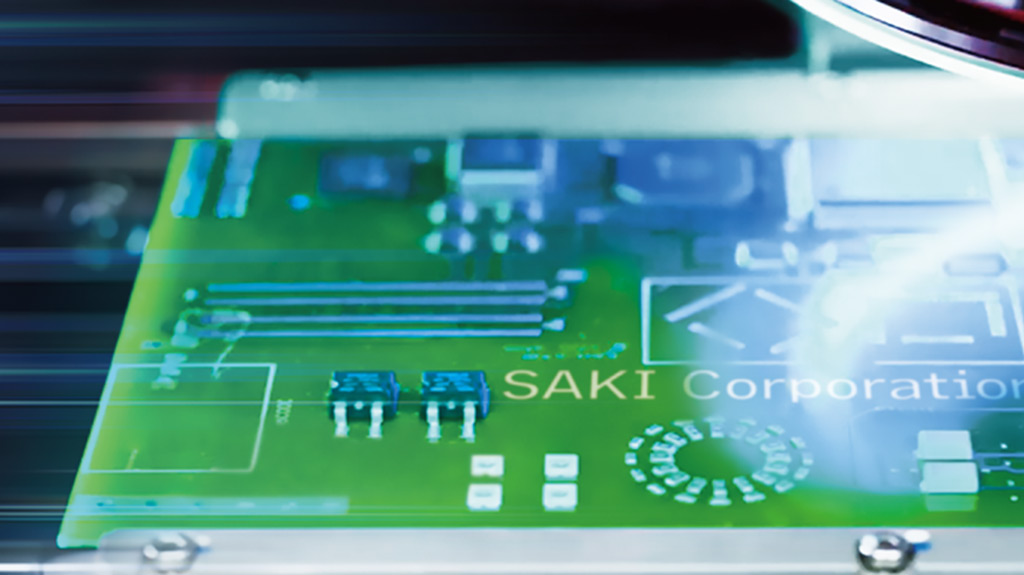
3D Image Acquisition Technology
Many of Saki’s original image processing technologies are used to obtain clear 3D images of the entire board surface.
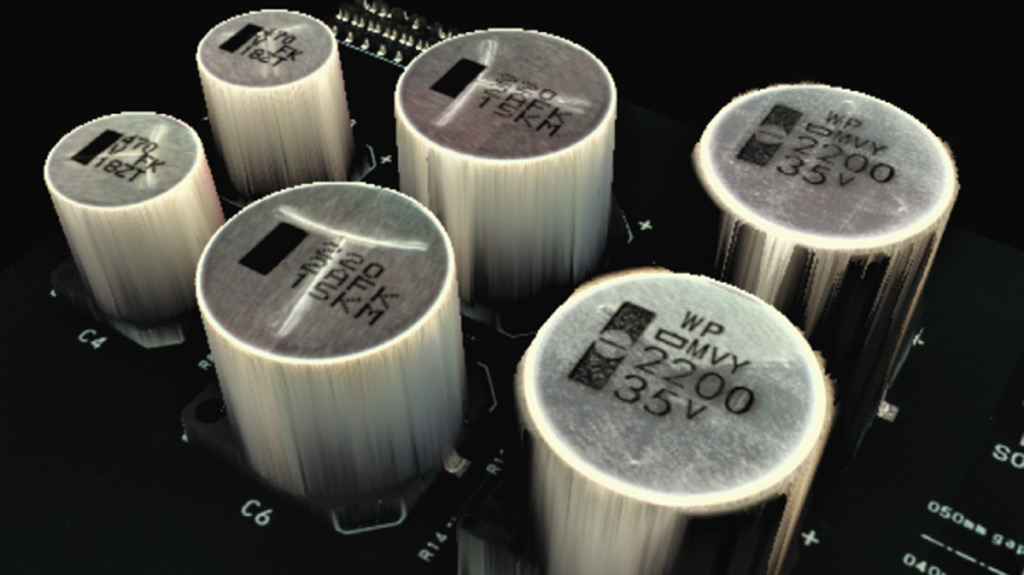
inview trigger
Product
3D-SPI
3D Solder Paste Inspection Machine

3D-AOI
3D Automated Optical Inspection Systems

3D-CT AXI
Inline 3D-CT Automated X-ray Inspection Systems

2D-AOI
2D Automated Optical Inspection Systems

BottomSide-AOI
Inline Bottom-side 2D Automated
Optical Inspection Systems

Power Module AXI
Inline 3D X-ray Inspection Machine for IGBT Power Modules

inview trigger
News release / Announcement
-
2024/04/16AnnouncementJarda Neuhauser, General Manager of Saki Europe, joins panel debate on “AI and the role of Virtual Assist”
-
2024/04/08AnnouncementSaki celebrates its 30th anniversary
-
2024/04/04AnnouncementSaki’s website has opened German and Korean language versions
-
2024/03/13News releaseSaki to Unveil Cutting-Edge Inspection Innovation to US-Market at IPC APEX Expo 2024
Event
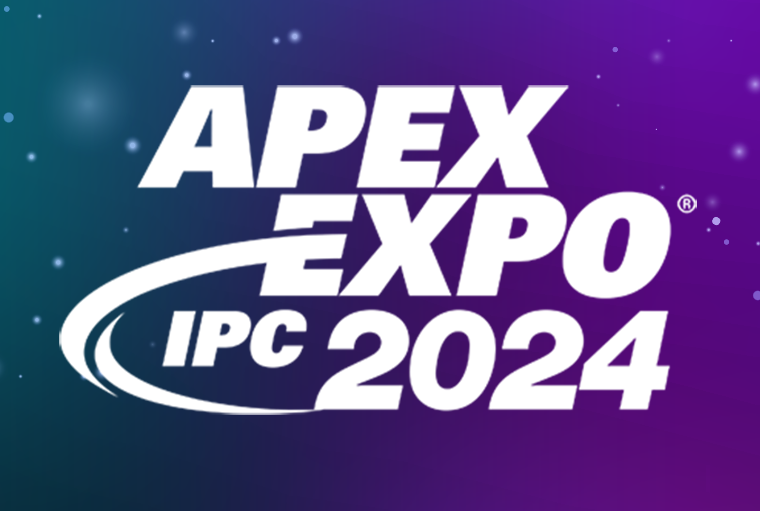
IPC APEX EXPO 2024
Date
2024/04/09 – 04/11
Venue
Anaheim Convention Center
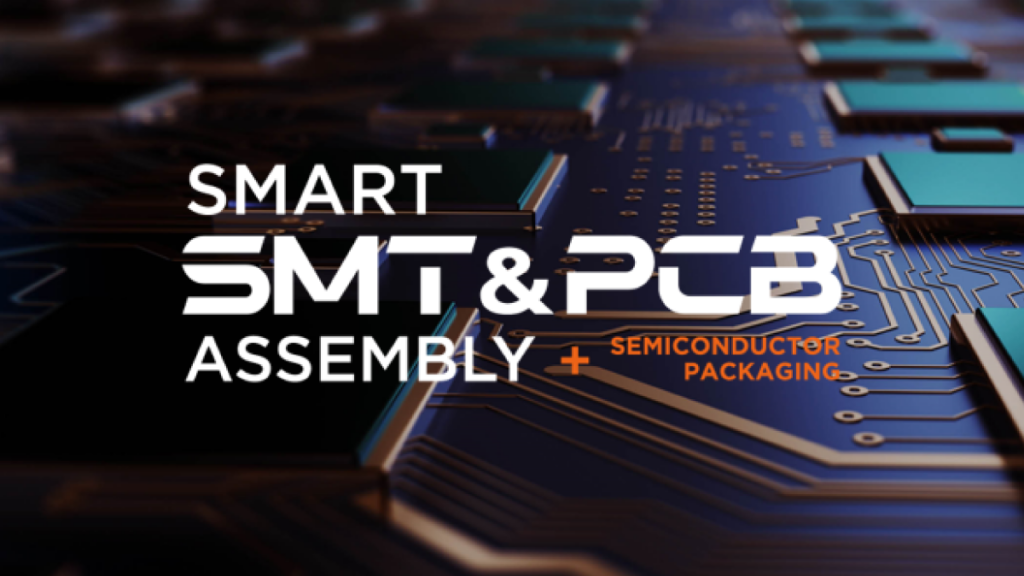
Smart SMT & PCB Assembly 2024
Date
2024/02/21 – 02/23
Venue
Suwon Convention Center

38th NEPCON JAPAN
Date
2024/01/24 – 01/26
Venue
Tokyo Big Sight

productronica 2023
Date
2023/11/14 – 11/17
Venue
Trade Fair Center Messe München

productronica India 2023
Date
2023/09/13 – 09/15
Venue
BIEC, Bengaluru

FIEE 2023
Date
2023/07/18 – 08/21
Venue
São Paulo Expo
About Us
Saki is a leading manufacturer of automated electronic assembly inspection equipment. Saki provides quality inspection solutions that determine a product’s viability by capturing and analyzing detailed imagery of the printed circuit board and components, replacing manual visual inspection with a highly accurate automated process. With a focus on power semiconductors and electronic substrates, Saki’s equipment delivers premium quality assurance for the electronic modules that are essential to the manufacture of electrical products.
Global Network
